Ball Mills Manufacturers – BALL MILLS
Ashoka is one the leading Ball Mills Manufacturers In India, the ball mill is a horizontal cylindrical shaped equipment used for grinding hard minerals to power fines. These are widely used for the cement, silicates, building materials, black and non-ferrous metals, ceramics and etc.
Common applications for our ball mills is grinding of clinker for cement manufacturing, mineral ore’s, calcium bauxites, silicates and other materials that can be ground into fines either by wet process or by dry process. Balls mills are divided into multiple chambers (generally two or three chambers) along its length.
The chambers are divided by diaphragms. Ashoka India manufacturers each chamber offers grinding to a particular size and the subsequent chamber makes the particle size finer in terms of diameter. They are cladded with liners throughout the internal periphery of the mill as well as the chamber dividing diaphragms.
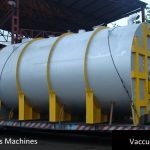
Ball Mills Manufacturers Working Principal
A ball mill grinds material by rotating a cylinder with steel grinding balls/ceramic balls causing the balls to fall back into the cylinder and onto the material to be ground. The cylinder rotates at a relatively speed, allowing the balls to cascade through the mill base, thus grinding or dispersing the materials. The rotation is usually between 4 to 24 revolutions per minute, depending upon the diameter of the mill.
The larger the diameter, the slower the rotation. If the peripheral speed of the mill is too much, it begins to act like a centrifuge and the balls do not fall back, but stay on the perimeter of the mill. The point where the mill becomes a centrifuge is called the “Critical Speed”, and ball mills usually operate at 65% to 75% of the critical speed. The critical speed (rpm) is given by: nC = 42.29/√d, where d is the internal diameter in metres. So a mill with diameter 5 metres will turn at around 14 rpm.
Ball mills are generally used to grind material 1/4 inch and finer, down to the particle size of 20 to 75 microns. To achieve a reasonable efficiency with ball mills, they must be operated in a closed circuit system, with oversize material continuously being re-circulated back into the mill to be reduced. Various classifiers, such as screens, cyclones and air classifiers are used for classifying the discharge from ball mills.
Balls mills are divided into multiple chambers (generally two or three chambers) along its length. The chambers are divided by diaphragms. Ashoka India manufacturers each chamber offers grinding to a particular size and the subsequent chamber makes the particle size finer in terms of diameter. They are cladded with liners throughout the internal periphery of the mill as well as the chamber dividing diaphragms.

Design Features
The horizontal cylinder of the ball mill, which is fabricated out of mild steel plates, is rotated using a side drive system at one end of the mill. The drive comprises of a girth gear, generally made from alloy steel casting, bolted onto the mill which is driven by its pinion, generally made out of alloy steel forging, through a gear reducer and motor coupled together.
The two ends of the cylinder are covered with mill ends (also called mill headers) one placed at each end, the inlet and at the discharge. The mill ends have a central inlet and discharge opening from where the material enters the mill and exits the mill. These mill ends (mill headers) are generally made out of alloy steel casting. The mill headers are rested on fabricated trunions at both ends on which the headers rotate on a special self lubricating white metal lining. External lubrication system is also provided to keep the mill headers properly lubricated at all times. Other accessories include a set of low pressure and high pressure pumps which help to pre-jack the mill during startup. Ball Mills Manufacturers.

Grinding Media
A ball mill is partly filled with steel balls (some are cylindrical shaped cylpebs) that impart a tumbling and cascading action when the mill rotates around its horizontal axis. Material fed through the mill is crushed by impact and ground by attrition between the balls. The grinding media are usually made of high-chromium steel or manganese steel. The smaller grades are generally cylpebs.
The mill is usually divided into at least two chambers, allowing the use of different sizes of grinding media. Large balls are used at the inlet, to crush clinker nodules (which can be over 25 mm in diameter). Ball diameter here is in the range 60–80 mm. In a two-chamber mill, the media in the second chamber are typically in the range 15–40 mm, although media down to 5 mm are sometimes encountered. As a general rule, the size of media has to match the size of material being ground: large media can’t produce the ultra-fine particles required in the finished cement, but small media can’t break large clinker particles. Mills with as many as four chambers, allowing a tight segregation of media sizes, were once used, but this is now becoming rare. Ball Mills Manufacturers.
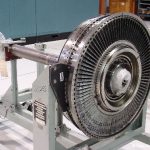
Mill Liners
As explained earlier all ball mill that Asoka India manufacturers are cladded with liners throughout its periphery of the length. Mill liners are generally of high chromium steel or manganese steel. The liners are selected based on the type and hardness of the material to be ground.
The grinding media is also selected with the same principal and suitable to the material of the liners. The thickness and design of the liners largely effect the grinding efficiency of the mill and hence various improvements in the designs have been made from time to time. Ball Mills Manufacturers.
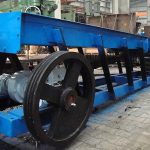
Closed Circuit Mill
The efficiency of the early stages of grinding in a ball mill is much greater than that for formation of ultra-fine particles, so ball mills operate most efficiently by making a coarse product, the fine fractions of this then being separated, and the coarse part being returned to the mill inlet.
The proportion of the mill-exit material returned to the inlet may vary from 10-30% when ordinary cement is being ground, to 85-95% for extremely fine cement products. It is important for system efficiency that the minimum amount of material of finished-product fineness is returned to the inlet. Modern separators are capable of making a very precise size “cut” and contribute significantly to the reduction of energy consumption, and have the additional advantage that they cool both the product and the returned material, thus minimizing overheating. Ball Mills Manufacturers.